Gibson Custom Shop
Setup Tips
It’s your guitar; don’t be afraid to work on it.
The Gibson Custom Shop builds the finest electric guitars ever
made. Whether painstakingly recreating the sought-after classics of the
late 50s and early 60s with the incredible VINTAGE ORIGINAL SPEC series,
or enhancing time-honored traditions to an artist's wishes with the
INSPIRED BY models, the luthiers of Gibson Custom have elevated guitar
building to both a science and an art. It is a labor-intensive, hands-on
process from start to finish, and each guitar brings with it special
requirements and demands. They all have something in common, though:
Before a guitar can leave the Custom Shop, it is meticulously set up to
play beautifully.
Here, for the first time, is an intensive breakdown of a Gibson
Custom Shop setup process. Many players don't realize that a guitar is a
precision instrument. Change in season, temperature, humidity, and even
playing style can radically change a guitar's playability. While a
guitar store or guitar repairman can set up your guitar for you, this
will cost you anywhere from $25 to over $100. Also, much of a setup is
based on your own personal preferences. Nobody can know your guitar like
you do, and doing your own setups will allow you to know your guitar
even better. The luthiers of the Gibson Custom Shop recommend setting up
your guitar at least twice a year, more if you live somewhere with
strong climate changes.
A setup is a simple process once you get the hang of it. Work
slowly and consult the pictures. Note that extreme care must be taken
when tightening the truss rod. This is one of the few things you can do
during a setup that can actually ruin your guitar. Remember, your guitar
is a precision instrument. All the steps of the setup are designed to
be performed slowly and gently. The results will be improved sound and
playability, and a closer relationship with your instrument.
YOU WILL NEED:
- Wire cutters for strings
- String winder
- WD40 to oil truss rod nut
- Small thin-walled 7/16" nut driver to adjust truss rod
- Small phillips-head screwdriver to remove truss rod cover and small flat-head screwdriver to adjust intonation
- 0000 steel wool
- Fine, soft paintbrush
- Linseed oil
- 6" ruler, with measurements in 64ths
- Tuner
- Dry rag
| 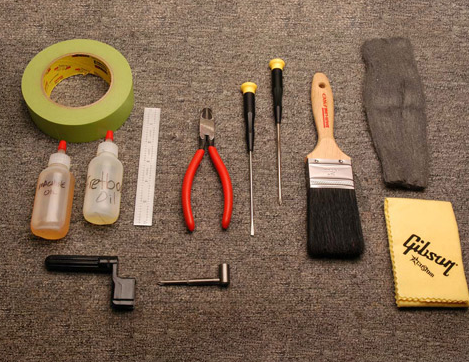 |
STEP 1
Remove strings.
STEP 2
Gently clean frets and fretboard with 0000 steel wool. Place a
little tape over the neck pickup to prevent steel wool from getting into
the coils. With a soft paintbrush, thoroughly clean dust and dirt off
neck after steel wooling.
Note: If you are steel wooling the frets on a maple board, cover the fretboard with masking tape to protect it from scratches.
| 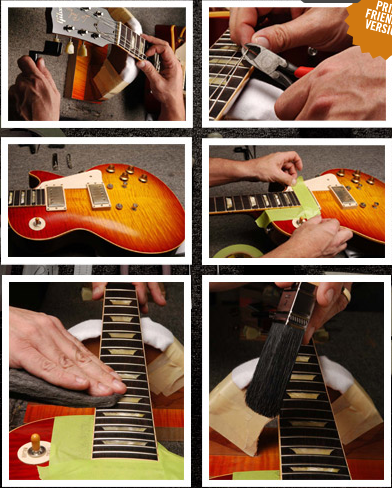 |
STEP 3
Apply a light layer of linseed oil to the fretboard to bring out
the deep richness of the rosewood. Immediately clean oil off fretboard
with a dry rag. Be sure to remove all oil. Use linseed sparingly. An
average-sized can of linseed oil should last years.
STEP 4
Restring, tune to pitch.
STEP 5
To check neck straightness and relief, hold the low E string down
directly on top of the 2nd fret and directly on top of the last fret at
the body (the 16th). Using the low E string as a straight edge, check
the distance around the 7th and 9th frets. The string should just be
clearing the frets by a hair.
| 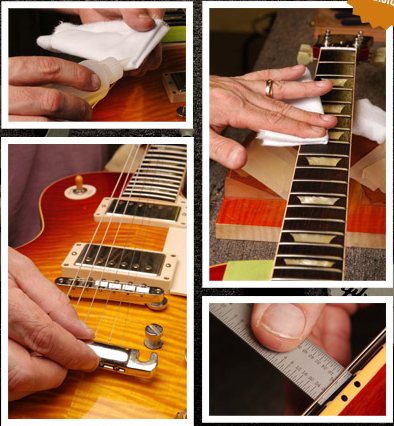 |
STEP 6
If your neck needs to be adjusted, gently loosen the truss rod, by
turning counter-clockwise. If it is tough to turn, remove truss rod nut
and place a small drop of oil on truss rod thread. WD40 or machine oil
will work fine, but do not spray it directly on the thread. Spray a
little into a cup and dab on a couple drops with a Q-Tip. Apply just
enough oil to lightly coat the thread. Gently adjust clockwise until the
truss rod nut is just snug, turning in quarter turns, until the
fretboard is straight and flat. When neck is straight, the low E string
will run flat against the top of the frets. Then back off 1/8 of a turn
counter-clockwise for slight relief.
| 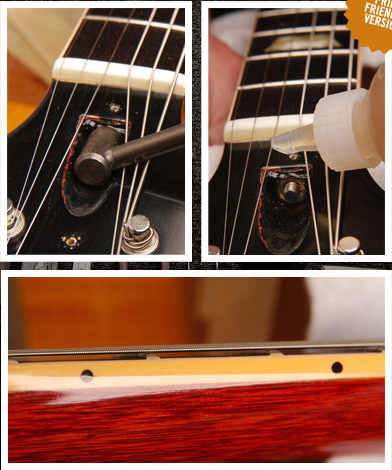 |
STEP 7
Adjust action by turning the wheels on the ABR or Tune-O-Matic
bridge. From the top of the first fret to the bottom of the string, from
high E to low E, the approximate measurements will be: high E: 1/64”,
B: 1/64”, G: 1.5/64”, D: 1.5/64”, A: 2/64”, low E: 2/64”. At the 12th
fret, the approximate measurements will be 3/64” for the high E string,
and 5/64” for the low E string. Tailpiece should be flush to the body
when using an ABR-1, and slightly higher for a Tune-O-Matic (just enough
for the strings to clear the back of the bridge).
STEP 8
Set intonation screws on the bridge. To rough in the intonation,
center the low E and high E saddles to the post holes in the bridge. The
A string will be 2/32” closer to the nut than the low E and the D
string will be 2/32” closer to the nut than the A. The B string will be
2/32” closer to the bridge than the high E and the G string will be
2/32” closer to the bride than the B string. These measurements will get
you in the ball park. Intonation will vary with instruments and string
gauges.
| 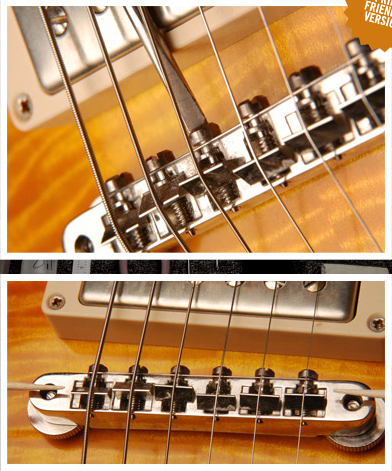 |
STEP 9
Final intonation. Adjust in playing position! Plugged into a
tuner, sound the string open and then fret the string at the 12th fret.
The note should be exactly one octave higher when fretted. If the note
is sharp at the 12th fret, adjust the saddle so it is closer to the
tailpiece. If it is flat, adjust the saddle to be closer to the nut.
STEP 10
Set pickup height. Fret on the last fret of the guitar. Pole pieces should be 3/64” from the bottom of the string.
| 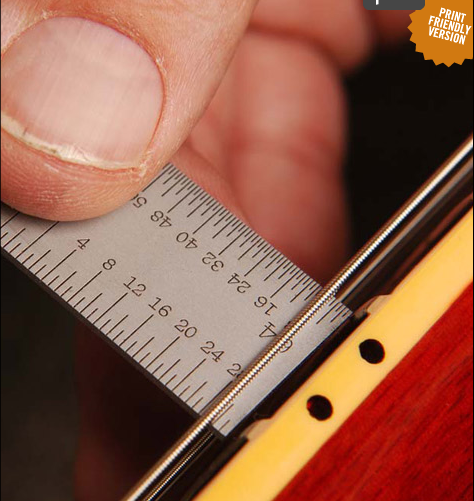 |
STEP 11
Plug in, play, enjoy
| 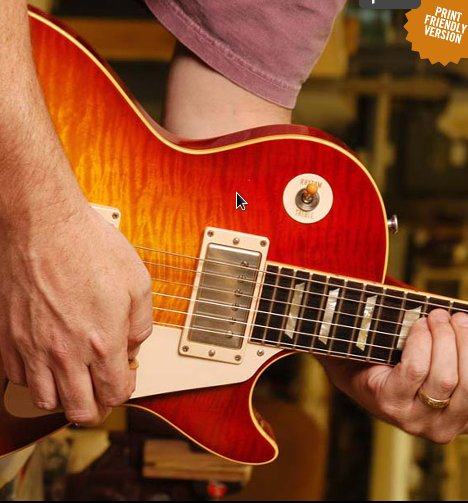 |
|